設計のためにアルミ棒の成形が必要ですが、うまくできるか心配ですか?欠陥のない正確な曲げ加工を実現するのは、経験や適切なセットアップがないと難しいように思われるかもしれません。
カスタムアルミニウム部品を供給している私の経歴からすると、アルミニウムロッドの曲げ加工には、特定のテクニックと材料を理解することが必要です。その難易度は、合金、調質、直径、希望する曲げ半径に大きく依存しますが、正しいアプローチと知識があれば、間違いなく達成可能です。
アルミ棒の曲げ加工に成功すると、構造部材や骨組みから装飾品や機能部品まで、さまざまな用途が広がります。ここでは、曲げ加工の難易度、成功のために必要な道具、避けるべき一般的な落とし穴、そしてこの万能棒を曲げることができる限界について見ていきましょう。
アルミ棒を正確に曲げるのは難しいですか?
ロッドを曲げるプロジェクトを始めるのは気が引けるものだ。素材を台無しにすることなく、正確なカーブを描くのはどれほど難しいことか。私はよく、デザインを計画しているクライアントとこのことについて話し合います。
私の経験では、難易度は大きく異なる。柔らかくて小径のロッドを大きな半径に曲げるのは非常に簡単です。しかし、より硬い合金や大きな直径を正確に曲げたり、きつい半径を達成したりするには、より高度な技術や適切な工具、問題を防ぐための慎重な管理が必要です。
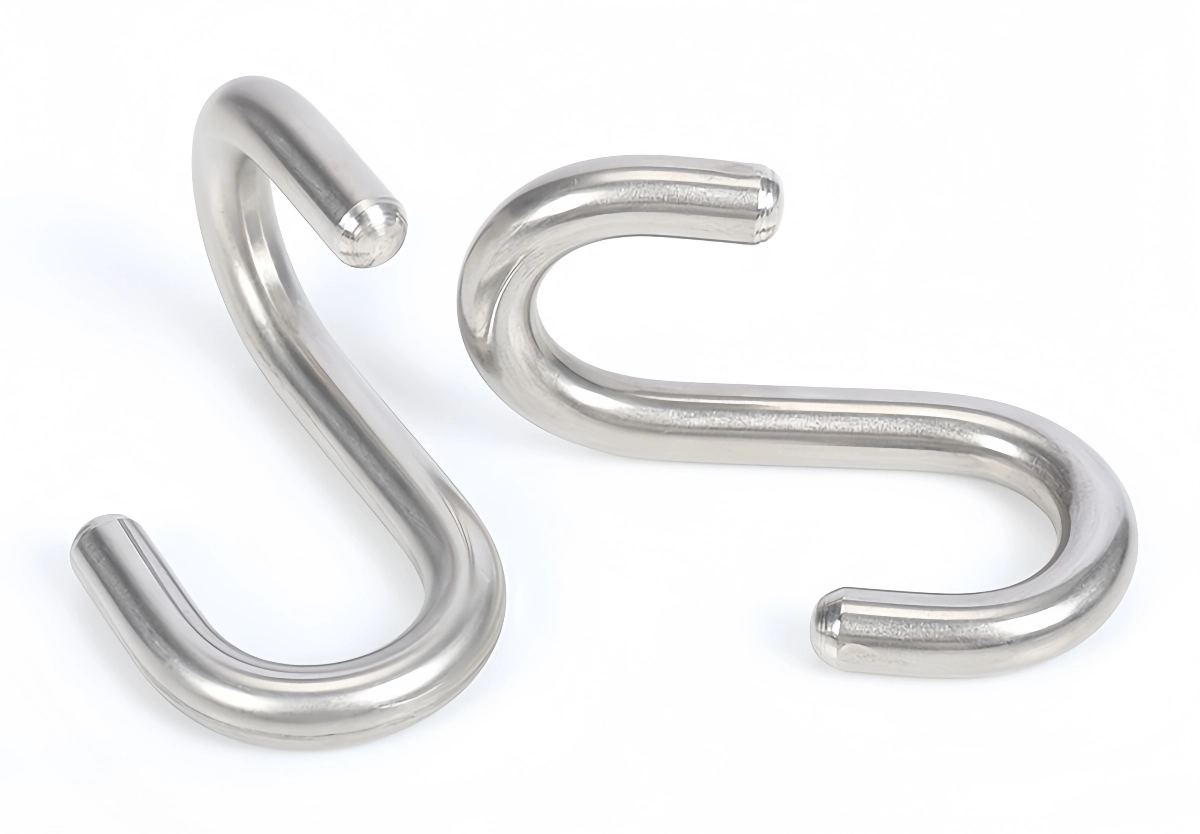
アルミ棒を正確に曲げることの難易度は、相互に関連するいくつかの要因に大きく左右されます。この作業は、比較的簡単なものから、かなり困難なものまであり、高い方では専門的な知識と設備が要求されます。
曲げ難さに影響を与える要因
- アルミニウム合金: 異なるアルミニウム合金は、その成形性に直接影響する、大きく異なる機械的特性を有しています。
- より軟らかい合金(例:1100、3003): これらの合金は降伏強度が低く、延性(伸び)が高い。つまり、少ない力で容易に変形し、外側の曲げ部分でも割れることなくかなり伸びる。これらの曲げ加工は一般的に容易とされている。
- 中強度合金(5052、6063など): 強度と成形性のバランスがとれている。1XXXシリーズや3XXXシリーズよりも強い力が必要だが、特に軟らかい調質材では容易に曲げられる。
- 高強度合金(例:6061-T6、2024、7075): これらの合金は著しく強く、延性が低い。曲げ加工に大きな力を必要とし、割れやすく(特に曲げ半径の外側で)、曲げ半径を大きくする必要があります。これらの合金を欠陥なく正確に曲げるには、堅牢な設備と慎重な工程管理が必要です。
- 気性が荒い: どのような合金(特に6061や6063のような熱処理可能な合金)でも、調質(熱処理や加工硬化によって達成される硬度/強度レベル)が重要である。
- O'テンパ(アニール処理): 最も柔らかく、最も延性のある状態。どのような合金でも、常に最も曲げやすい調質。
- T4テンパ: 固溶化熱処理と自然時効処理。O'よりも強度が高いが、T6よりも成形性が高い。
- T6テンパー 溶体化熱処理と人工時効処理により強度を最大化。この処理により延性が著しく低下するため、T6は曲げ加工が最も難しい一般的な調質材となる。
- ロッドの直径: 直径の大きい棒材は、同じ合金や調質の直径の小さい棒材よりも、変形する材料の量が増えるだけで、曲げ加工に必要な力は本質的に大きくなります。曲げ装置は、必要な力に対して適切な大きさでなければなりません。
- 曲げ半径: 材料がその合金、調質、直径に対応できる半径よりもきつい半径にロッドを曲げようとすることは、困難と破損(亀裂/破断)の主な原因である。よりきつい曲げは、材料により大きなひずみを与える。非常にきつい半径を正確に達成することは、常により困難である。
- 精度の要件: ロッドをおおよそのカーブに曲げるのは、精密な角度と半径を厳しい公差で実現するよりも簡単で、より高度な工具と測定が必要になる。
一般的な難易度
困難は概念的にまとめることができる:
シナリオ | 難易度 | 主な課題 |
小径、軟質合金(3003-O)、大R | 簡単 | 最小限の力、低い割れリスク |
中径、中合金(6061-T4)、中程度の半径 | 中程度 | 適切な工具、適度な力、スプリングバックが必要 |
大径、硬質合金(6061-T6)、タイトな半径 | 難しい | 力が強く、クラックのリスクが高いため、精度が要求される。 |
従って、アルミニウム棒を曲げながら 缶 有利な条件下では容易であるが、より強い合金、より大きなサイズ、または狭い半径で正確な曲げを実現するには、適切な知識、工具、および技術を必要とする重大な課題がある。
アルミ棒を適切に曲げるには、どのような工具を使うのですか?
曲げ加工は難しいものだが、ロッドを傷つけずに正しく曲げるには、どんな道具が必要なのだろうか?その場しのぎの方法に頼ると、悪い結果につながることがよくあります。
製造の観点からは、回転式ドローベンダー、3本ロールベンダー、油圧プレスブレーキなどの特殊工具を使用し、特定のロッド径と希望の半径に合わせて設計された適切な金型を使用します。小さくて柔らかいロッドには、ハンド・ベンダーもあります。
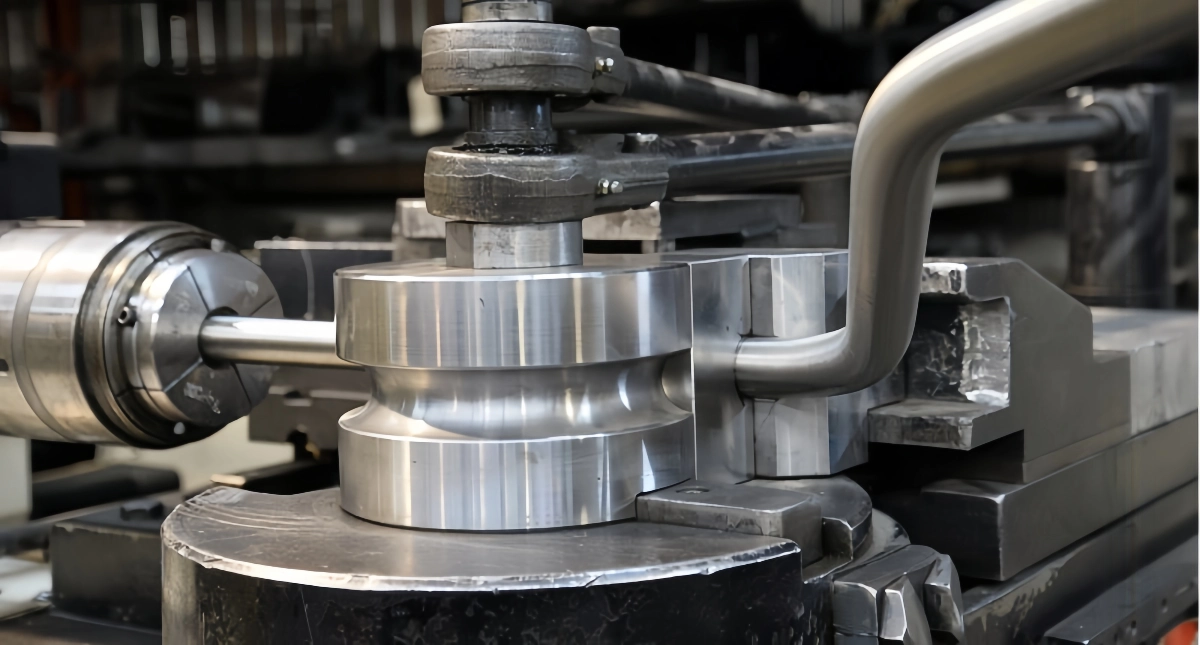
アルミニウム棒の曲げ加工を、特に精度よく、欠陥なく成功させるには、通常、この作業用に特別に設計された工具が必要です。工具の選択は、ロッドの直径、合金と調質、必要な曲げ半径と角度、必要な精度、生産量によって大きく異なります。バイスや力技を使ったその場しのぎの方法では、ねじれや不正確な曲げ、破断につながることがよくあります。
一般的な曲げ工具
- ハンドヘルド・チューブ/ロッド・ベンダー:
- 説明 手動工具で、多くの場合レバーで操作し、小径のロッド(合金の軟らかさにもよるが、通常1/2インチまで、またはそれよりわずかに大きい)用に設計されている。通常、一般的な半径の溝やダイスがあらかじめ形成されている。
- 最適: 軟質合金(1100、3003、軟質5052/6063)、小径、非重要曲げ、DIYプロジェクト、現場修理、少量生産。
- 制限: 力が限られているため、より強い材料で高精度や厳しい半径を達成するのは難しく、オペレーターの技量に大きく依存する。
- ロータリー式ドローベンダー:
- 説明 ロッドをクランプし、回転する曲げダイスの周囲に引き回す、より高度な機械(手動、油圧、またはCNC)。内部マンドレル(ソリッドロッドの場合、チューブより一般的ではない)やワイパー/加圧ダイを使用し、曲げ加工中に材料を支持することが多い。
- 最適: 高精度、一貫性、高品質の曲げ加工を、特に半径の狭い材料や難度の高い材料で実現。中~大量生産に適しています。CNCバージョンは、複雑なマルチベンドシーケンスを可能にします。
- 制限: ロッド径や曲げ半径に応じた金型が必要で、初期設備コストが高い。
- 三本ロールベンダー(アングルロール、セクションベンダー):
- 説明 3つの調節可能なローラー(通常はピラミッド型)を備えた機械で、ロッドがその中を何度も通過する際に徐々にカーブする。
- 最適: 大きな半径のベンド、スイープカーブ、円弧、スパイラル、または完全な円の作成。機械の能力に応じて、さまざまなサイズのロッドに対応。
- 制限: 狭い半径には適さない。曲げの始点と終点を正確にするのは、ドロー曲げに比べて難しい。
- 油圧プレスブレーキ(Vダイまたはラジアスツーリング付き):
- 説明 主にシートメタルに使用されますが、適切なVダイまたは特殊なR工具を装備したプレスブレーキは、ロッドの曲げ加工にも使用できます。
- 最適: 構造用ブラケットやサポートによく使用される、ロッドの不連続なアングル曲げの作成。直径が大きく、大きな力を加えることができる。
- 制限: ロールベンダーやドローベンダーに比べ、滑らかで連続的なカーブには不向き。
- カスタム治具と治具:
- 説明 特定の繰り返し曲げ加工には、ロッドをガイドする特注の治具を製作し、手作業やより簡単な曲げ加工法を使用する際の一貫性を確保することができる。
- 最適: 特定の部品形状に対するローテク曲げセットアップの再現性を向上させる。
- 制限: それぞれのユニークな曲げに設計と製作が必要。
必須工具部品(機械曲げ用)
- ベンド・ダイ: ロッドが適合する所望の半径を持つ第一の工具。
- クランプダイ: 曲げ加工中にロッドの直線部分を確実に保持する。
- プレッシャーダイ: ベンド・ダイの周囲に引き出されるロッドを支えるために圧力を加える。
- (オプション)マンドレル: 主にチューブに使用される内部サポートだが、あまり一般的ではないが、特定のロッド曲げのシナリオに適応することもある。
- (オプション)ワイパーダイ: シワを防ぐため、接線のすぐ先で内半径を支える(チュー ブの場合はより重要)。
適切な工具の選択には、工具の能力(力、精度、半径容量)と特定の曲げ作業の要求(材料、直径、曲げ要件)を一致させることが含まれます。サイズが小さかったり、不適切な工具を使用することは、結果が悪くなる一般的な原因です。
アルミ棒の曲げ加工でよくある失敗とは?
道具と材料は揃いました。実際にロッドを曲げるときに大きなミスをしないためには、どんな落とし穴に気をつければいいでしょうか?
多くの試行錯誤を見てきたが、よくある失敗としては、間違った合金/テンパーの選択(硬すぎる)、最小半径よりきつく曲げること、不適切な工具や破損した工具の使用、力のかけすぎ、ねじれや破損につながる不十分なサポートなどがある。
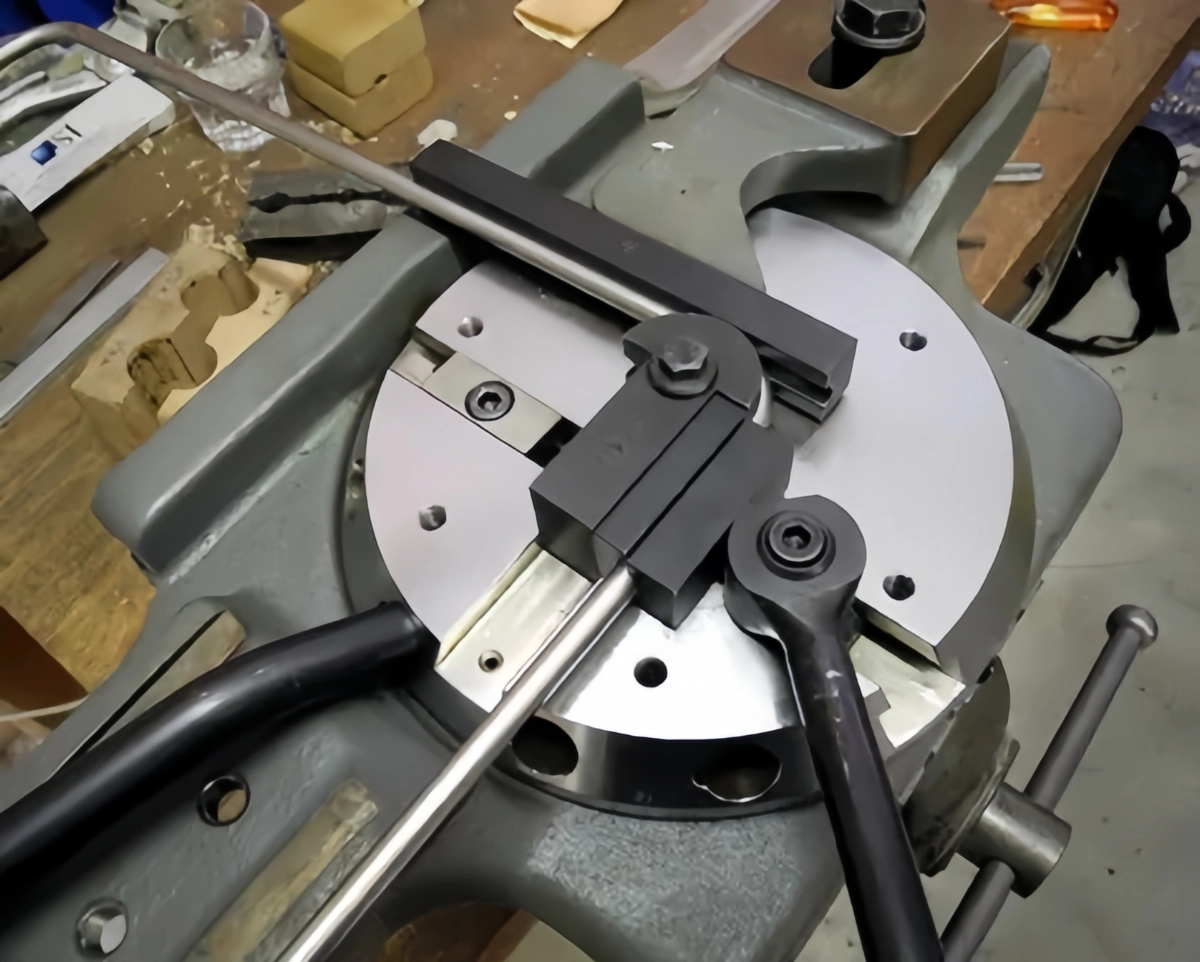
アルミ棒の曲げ加工は簡単なように思えますが、よくある間違いが、部品のひび割れ、不正確な寸法、表面の損傷、一貫性のない結果など、望ましくない結果につながることがあります。これらの落とし穴を認識することが、高品質の曲げ加工を実現するための第一歩です。
間違い1:誤った材料/テンパー選択
- エラー: 意図した曲げ半径や成形工程に対して、硬すぎたり、延性が十分でない合金や調質材を選択すること(例えば、6061-T6できつい曲げを作ろうとすること)。
- 結果 曲げ加工中の亀裂や完全な破壊、過大なスプリングバック、過大な力を必要とし、工具や部品を損傷する可能性がある。
- 予防だ: 材料の仕様書を参照すること。3003、5052、6063/6061のような合金で、より軟らかい調質(O、T4、Hx2/Hx4)のものを大きな曲げのために選択する。最終強度と成形性のトレードオフを理解する。
間違い2:最小曲げ半径違反
- エラー: ロッドの直径、合金、調質において、材料が安全に許容できる半径よりも小さな半径でロッドを曲げようとすること。
- 結果 外側の曲げ面に高い引張応力がかかると、亀裂や破断が生じます。曲げ内面に強い圧縮がかかると、座屈やひずみが生じます。
- 予防だ: 常に、特定の材質の状態に対して推奨される最小曲げ半径を決定し、それに従ってください。適切な半径の工具を使用してください。一般に、柔らかい素材や温度では、よりタイトな半径が許容される。
間違い3:不適切または破損した工具の使用
- エラー: ロッドの直径用に設計されていない工具の使用、摩耗または損傷したダイスの使用(くぼみ、粗い表面)、その場しのぎのセットアップ(万力で鋭利なエッジを折り曲げるなど)。
- 結果 キンク、扁平(楕円、ただしソリッドロッドではチューブより顕著ではない)、表面損傷(傷、溝)、不正確な曲げ角度や半径。工具の損傷は、亀裂につながる応力上昇を引き起こす可能性がある。
- 予防だ: ロッドの直径と曲げタイプに合わせて特別に設計された工具を使用すること(回転式ドローベンダー・ダイ、ロールベンダー・ロールなど)。工具が滑らかで、サイズが正しく、良好な状態であることを確認する。適切なサポートダイ(プレッシャーダイ)を使用する。
間違い4:不十分なマテリアル・サポート
- エラー: 曲げ加工中、特に曲げ部付近でロッドを適切に支持しな かった場合(プレス曲げやあまり高度でない方法に関連する)。チューブの場合、必要なときにマンドレルを 省略することも含まれる。
- 結果 ロッドプロファイルのキンク、座屈、崩壊。
- 予防だ: ロッドの形状をサポートするプレッシャー・ダイスを使用した回転ドロー曲げのような方法を使用する。適切なクランプを確保すること。チューブの場合、きつい曲げや薄肉にはマンドレルを使 用する。
間違い5:間違った曲げ速度
- エラー: 特に延性の低い合金や複雑な曲げでは、曲げ力を急激にかけすぎる。
- 結果 材料への応力が増加し、亀裂や裂けが発生する可能性が高くなる。スプリングバックが一定でないため、最終角度のコントロール性が低下する。
- 予防だ: 材料と加工方法に適した、滑らかで制御された一定の曲げ速度を使用する。
間違い6:スプリングバックを考慮しない
- エラー: 弾性回復を考慮することなく、ロッドを希望の最終角度まで正確に曲げること。
- 結果 力を解放した後の最終的な角度が、意図したものよりも小さい。
- 予防だ: すべての素材にスプリングバックがあることを理解してください。スプリングバックは、ロッドをわずかに曲げ過ぎて補正する必要があります。必要な過曲げの量は、合金、調質、半径、角度によって異なり、多くの場合、試行錯誤や材料データを使った計算によって決まります。CNCベンダーは多くの場合、スプリングバック補正を自動的に計算して適用することができます。
間違い7:潤滑不足
- エラー: ロッドと工具(特にベンドダイとプレッシャーダイ)の間に適切な潤滑剤を使用しない。
- 結果 摩擦の増大は、曲げ力の増大、表面のかじり、ひっかき傷、工具の摩耗、そしてロッド表面の裂けや亀裂を引き起こす可能性がある。
- 予防だ: 摩擦を減らし、変形中の材料の流れを良くするために、アルミニウムに適合する適切な曲げ潤滑剤を塗布する。
慎重な計画、材料の選択、適切な工具、管理された技術によって、これらの一般的なエラーを回避することは、アルミニウム棒の曲げを成功させ、正確に行うために不可欠です。
アルミ棒を曲げる最小半径は?
私のデザインには本当にきついカーブが必要です。アルミ棒が折れたり、見た目が悪くなったりする前に、実際にどのくらい鋭く曲げることができますか?難しい限界はありますか?
最小曲げ半径は一律ではありません。私が扱っている材料仕様に基づくと、特定のアルミニウム合金、その調質、ロッドの直径に大きく依存します。O'調質で柔らかい合金であれば、ほぼゼロの半径で曲げられることもありますが、硬いT6では直径の5~8倍が必要になることもあります。
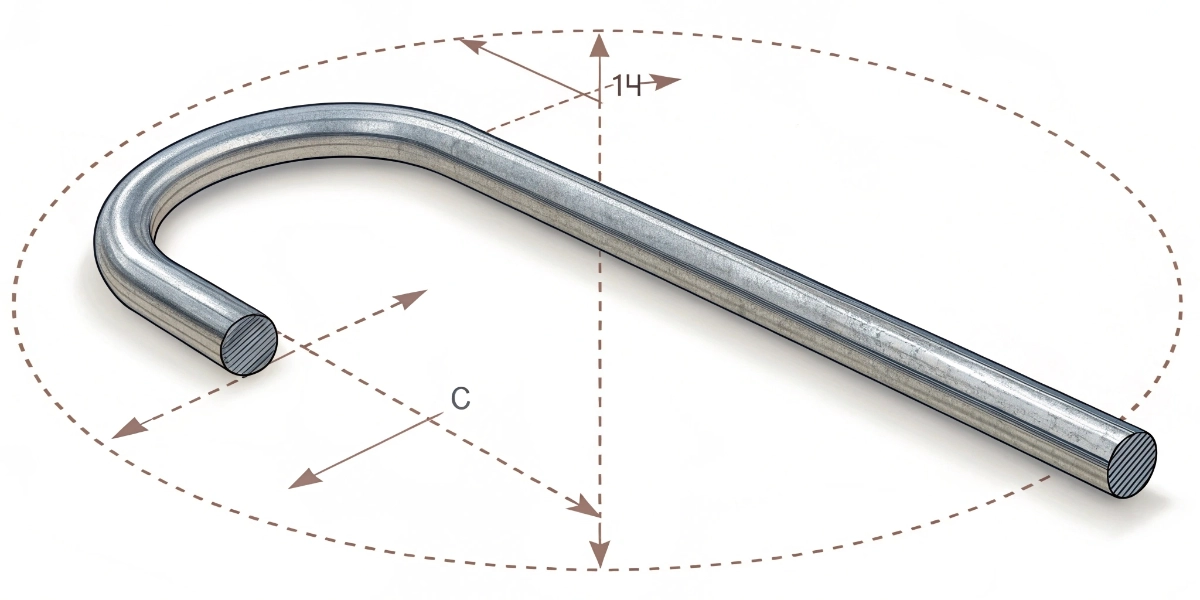
最小曲げ半径(MBR)は、アルミニウム棒を曲げた部品を設計する際に重要なパラメータです。これは、亀裂、過度の歪み、著しい弱化などの許容できない欠陥を引き起こすことなくロッドを曲げることができる最小の中心線半径を表します。MBRよりきつく曲げようとすることは、故障の一般的な原因です。
最小曲げ半径を決定する要因
MBRは固定値ではなく、主に以下の要因に左右される:
- アルミニウム合金とテンパー: これが最も大きな要因だ。
- 延性: 延性が高い(伸び率が高い)材料は、外側の曲げ面の伸びと内側の曲げ面の圧縮に耐えることができ、よりタイトな曲げを可能にします。焼きなまし(O調質)合金は最も延性が高い。
- 強さだ: 高強度合金(T6テンパーなど)は延性が低く、破断を避けるために曲げ半径を大きくする必要がある。
- ロッドの直径(D): シート/プレート/チューブの場合、厚さとの相対関係で 表すことが多いが、ソリッドロッドの場合は直径そのものがひずみに 影響を与える。しかし、MBRは直径に直接関係するよりも、材料の特性に関係することの方が一般的である。多くの場合、直径を基準としたガイドラインが示される(例:2D、3D半径)。
- 曲げ方法と工具:
- 方法だ: 適切なサポートがあれば、回転ドロー曲げのような精密な方法は、プレス曲げのような単純な方法と比較して、わずかにタイトな半径を達成できることが多い。
- 工具の品質: 滑らかで手入れの行き届いた工具は、応力の集中を最小限に抑える。
- 許容できる品質レベル: 許容できる」曲げの定義は、実用的なMBRに影響する。表面のわずかな欠陥やわずかな平坦化が許容できる場合は、完璧なプロファイルと仕上げが要求される場合よりも、わずかにタイトな半径が使用されるかもしれません。
一般的なガイドライン(概算)
MBRの値は特定の条件に依存するため、正確な値を示すことは難しいが、一般的なガイドラインは存在し、多くの場合ロッド直径(D)の倍数で表される:
合金/焼き戻し状態 | 典型的な最小曲げ半径(中心線) | 備考 |
非常に柔らかく、延性が高い: | | |
1100-O、3003-O | ~ 1Dから2Dへ | 鋭角に近い、非常にタイトなベンドにもよく対応できる。 |
ソフト/良好な延性: | | |
5052-o, 5052-h32 | ~ 1.5Dから3Dへ | 非常に優れた成形性で、曲げ加工部品によく使用される。 |
6061-O、6063-O | ~ 1.5Dから3Dへ | 焼鈍状態は、これらの合金にとって非常に成形しやすい。 |
中程度の強さ/まあまあの延性: | | |
6061-T4、6063-T4 | ~ 3Dから5Dへ | 曲げられるが、Oテンパーより大きな半径が必要。 |
高強度/低延性: | | |
6061-t6、6063-t6 | ~ 6Dから10D+まで | 強く曲げることが難しく、ひび割れの危険性が高い。 |
2024-T3/T4、7075-T6 | 非常に大きい / 推奨されないことが多い | 一般に、きつい曲げには不向きとされている。 |
重要な注意事項
- これらは 一般指針 のみ。可能であれば、必ずサプライヤーから入手した特定の材料データシートを参照するか、曲げ試験を行ってください。
- 曲げの質(滑らかさ、亀裂のなさ)が最も重要です。絶対的な最小値に近づけすぎると、完全性が損なわれる可能性がある。
- これらの半径は、適切な工具と技術が使用されていることを前提としている。
実践的な意味合い
- 設計段階: 設計者は、設計の初期段階でMBRを考慮しなければならない。材料が扱える曲げ半径よりも厳しい曲げ半径を指定すると、製造上の問題につながるか、より成形性の高い(そして潜在的に弱い)合金/調質材への切り替えが必要になる。
- 製造: オペレーターは、曲げ加工を行う特定のロッドのMBRを知り、工具とセットアップがこの制限を尊重するようにする必要があります。スプリングバックを補正するには、選択した半径での材料の挙動を理解することも必要です。
これらのガイドラインよりかなりきつく曲げようとすると、特に硬い合金や不十分な工具では、外面に目に見える亀裂が入ったり、ひどい場合にはアルミニウム・ロッドが完全に折れたりする可能性が高くなります。確信が持てない場合は、常に半径をわずかに大きくする側を選んでください。
結論
アルミ棒の曲げ加工の難易度は、合金、調質、サイズによって異なります。ドローベンダーのような適切な工具が鍵となります。最小曲げ半径を超えたり、間違った調質材を使用したりするような一般的なミスを避け、割れを防止し、設計に正確で信頼性の高い結果をもたらします。